5 Big Advantages of Aluminum Framing in Automotive Manufacturing
Introduction
The automotive industry thrives on speed, safety, and efficiency. Factories need materials that can withstand constant production, protect workers, and adapt quickly to changes. Aluminum framing is ideal for building workstations guardrails, storage systems, and more. Lightweight yet strong, aluminum framing delivers numerous benefits to automotive manufacturers.
Here are five key reasons why aluminum framing is a smart choice in the automotive industry.
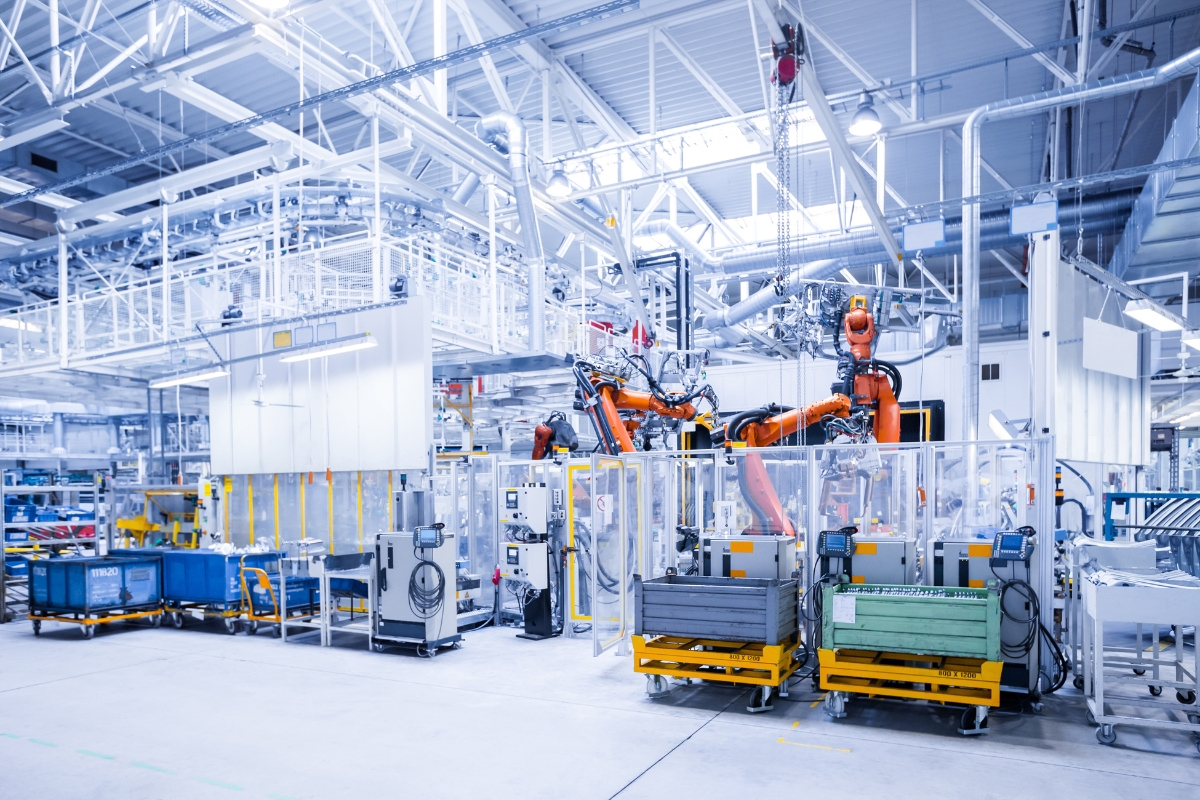
1. Strong and Built to Last
Automotive factories are busy, with heavy parts and equipment constantly on the move. The materials used for equipment and storage need to be strong and durable to handle this daily wear and tear. Aluminum framing fits the bill-it’s strong enough to support heavy loads without bending or breaking and doesn’t rust, even in humid or harsh environments.
Why does this matter? Durable materials don’t need to be replaced often, saving time and money. Aluminum framing’s strength allows it hold up well under stress, reducing maintenance and replacement needs. Since aluminum is rust-resistant, it’s an excellent choice for areas exposed to moisture, such as storage rooms or bustling production lines.
Example in action: Imagine a storage rack made from aluminum framing that holds heavy car parts in a plant. The aluminum can handle the weight without bending or rusting, so the rack lasts longer and doesn’t need constant repairs.
2. Flexible and Easy to Reconfigure
One of the biggest advantages of aluminum framing is its adaptability. Aluminum framing systems typically use T-slots, allowing components to connect or disconnect easily. This makes it simple for factories to adjust or rearrange workstations and equipment as needed, without specialized tools or a major rebuild.
Why is this important? Automotive manufacturing is always evolving. New car models, updated tools, and process changes mean factories must adapt quickly. With aluminum framing, manufacturers can move or adjust setups as needed without wasting time or money on new structures.
Example in action: If a car manufacturer needs to reconfigure a production line for a new model, they can easily adjust the aluminum framing setup to fit the new design. This flexibility reduces downtime and allows for a quick response to changing demands.
3. Enhances Safety and Comfort for Workers
Safety is crucial in automotive manufacturing, where workers often work near heavy machinery and moving parts. Aluminum framing helps create safer workspaces by making it easy to build guardrails, barriers, and enclosures around equipment. These protective structures reduce the risk of accidents and improve worker safety.
Why is this useful? A safer work environment leads to fewer injuries and less downtime. Aluminum framing can be quickly assembled to create barriers and guardrails wherever needed. It also supports ergonomic setups-workstations can be adjusted for different heights, reducing strain and helping workers stay comfortable and productive.
Example in action: Imagine a workstation where employees frequently reach for tools. With aluminum framing, the workstation height can be adjusted to match each worker, making it easier to access tools without bending or stretching too much. This reduces injury risk and boosts productivity.
4. Cost-Effective and Environmentally Friendly
Keeping costs low is essential, especially in competitive industries like automotive manufacturing. Aluminum framing offers long-term savings because it’s durable and modular, reducing the need for frequent replacements. Plus, aluminum’s lightweight nature makes it cheaper to transport.
Why does it matter? Lower spending on replacements and shipping means more resources can be invested in other areas. Aluminum framing is also recyclable, supporting the automotive industry’s shift towards sustainable practices.
Example in action: An automotive facility may need new racks for specific parts, but instead of purchasing completely new materials, they can reuse and reconfigure aluminum framing. When the racks are no longer needed, the aluminum can be recycled, reducing waste and supporting green initiatives.
5. Boosts Efficiency in Material Handling and Assembly
In automotive manufacturing, efficiency in material handling and assembly is crucial. Aluminum framing makes setting up custom storage racks, transport systems, and assembly stations easy, helping workers access parts and tools more quickly.
Why is this important? A well-organized and efficient workspace speeds up production. Aluminum framing allows for custom setups, ensuring tools and parts are within reach. Since aluminum is lightweight, these setups can be quickly installed and adjusted, keeping production lines running smoothly.
Example in action: Imagine a storage rack system with aluminum framing, designed specifically to hold parts fora particular car model. Workers can access the parts quickly, saving time and making the assembly process faster and more efficient.
Conclusion: Aluminum Framing is a Great Fit for Automotive Manufacturing
Aluminum framing has transformed automotive manufacturing by providing strong, adaptable, and sustainable solutions for workstations, guardrails, storage systems, and assembly lines. Its combination of durability, flexibility, and eco-friendliness makes it ideal for meeting the ever-changing demands of automotive production.
By choosing aluminum framing automotive manufacturers can create safer, more productive, and cost-effective workspaces. This choice supports both immediate productivity and long-term sustainability, helping companies stay competitive.
Interested in learning how aluminum framing can enhance your automotive facility? Pacific Integrated Handling specializes in custom aluminum framing solutions tailored to your unique needs. Contact us today to explore how we can help create a safer, more adaptable, and efficient workplace.
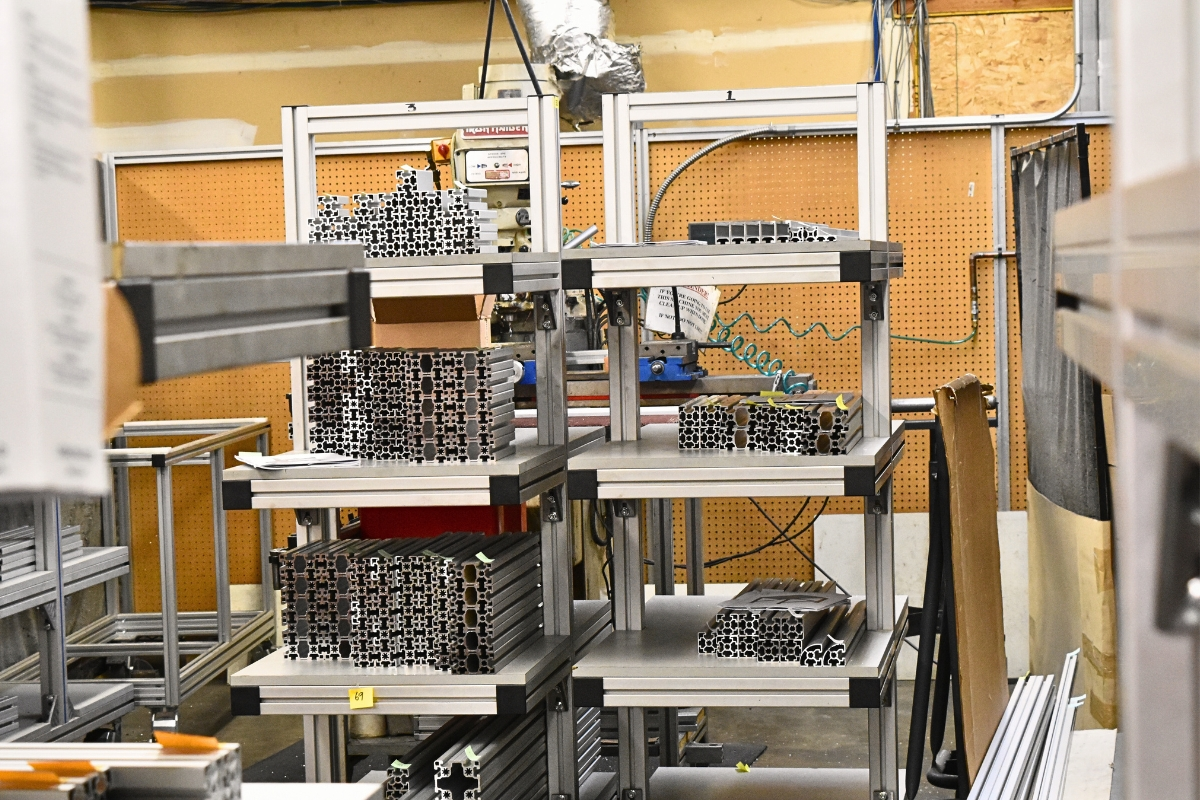