Introduction
The aerospace industry is among the most innovative, demanding, and high-stakes sectors, constantly pushing the boundaries of technology, precision, and safety. Aluminum framing, known for its versatility, strength-to-weight ratio, and modularity, has become crucial in aerospace applications. From assembly line efficiency to lightweight and durable structures, aluminum framing plays a pivotal role in meeting the rigorous demands of the aerospace field.
Here, we dive into hoe aluminum framing contributes to the aerospace industry’s needs and explore its advantages, applications, and future trends.
Why Aluminum Framing is Ideal?
Aluminum Framing is known for several properties that align perfectly with aerospace requirements.
Below are some of the primary reasons aluminum framing is favored in aerospace:
High Strength-to-Weight Ratio: Aerospace applications demand lightweight materials yet strong enough to handle high stress levels. Aluminum frames, with their excellent strength-to-weight ratio, are ideal for supporting heavy equipment and ensuring safe operations without adding unnecessary weight.
Corrosion Resistance: Aluminum is naturally resistant to corrosion, making it highly suitable for aerospace environments where equipment and components are exposed to varying altitudes, weather conditions, and other corrosive elements.
Modularity and Flexibility: Aerospace assembly and maintenance involve intricate processes that benefit from adaptable and customizable framing solutions. Aluminum framing can be easily configured, allowing for quick modifications, which is ideal for accommodating new parts, process adjustments, and updates in technology.
Durability: Aluminum framing is resilient and capable of withstanding extreme temperatures, vibrations, and other stresses common in aerospace environments. This durability ensures longevity, minimizing downtime and reducing maintenance costs.
Key Applications of Aluminum Framing
Aluminum framing systems have become integral across various aerospace applications. Some of the most notable areas where aluminum framing is used include:
Workstation and Assembly Areas
The complexity of aerospace assembly requires organized, functional, and flexible workstations. Aluminum framing enables engineers to design modular workstations that can be reconfigured based on project requirements. These workstations often come with tool and part storage, ensuring efficiency and safety during assembly and maintenance tasks.
Customizable Shelving & Racks
Storage is a crucial component of aerospace manufacturing and maintenance. Aluminum framing allows for highly customizable shelving and racks tailored to fit specific parts, tools, and equipment. This not only optimizes the use of space but also help keep essential items organized and easily accessible.
Equipment and Material Carts
Transporting materials and components within an aerospace facility requires carts that can handle varying loads and navigate safely through workspaces. Aluminum-framed carts are lightweight and can be customized to securely transport materials, improving efficiency and safety in the workflow.
Platforms and Elevated Work Surfaces
Assembly lines in the aerospace industry often need elevated work platforms to safely access aircraft or large machinery. Aluminum-framed platforms provide the strength required for worker safety while keeping the structure lightweight, making it easier to move, install, and adjust.
Guarding and Enclosures
Worker safety is paramount in aerospace operations. Aluminum framing is frequently used to build guarding and enclosure systems that protect personnel from hazardous machinery. These guard systems can be customized to fit specific machines or assembly areas, creating a safer work environment.
Testing and Simulation Equipment Frames
Aerospace companies rely heavily on testing and simulation to ensure equipment and components meet strict safety and performance standards. Aluminum framing structures are often used to house testing apparatus or simulate environments, providing the durability and customization needed for advanced aerospace testing.
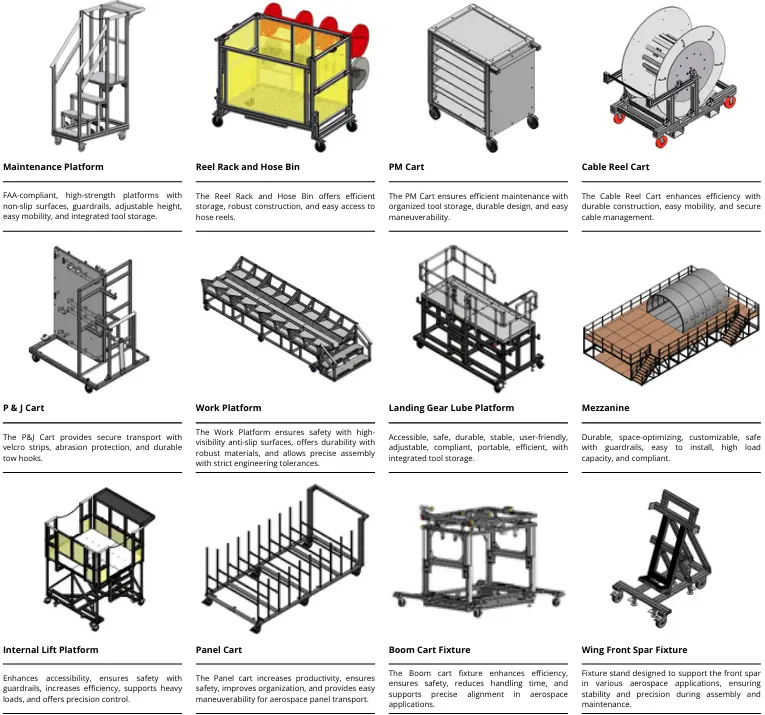
Advantages
Aluminum framing systems offer several advantages that are particularly valuable in aerospace:
Enhanced Efficiency
Aerospace projects require a high level of precision, which aluminum framing supports through its modular and easily adjustable design. Engineers can quickly adjust or reconfigure the framing for various applications, reducing assembly line, and boosting efficiency in both production and maintenance.
Cost-Effectiveness
Due to its durability and low maintenance requirements, aluminum framing offers a cost-effective solution over time. Its corrosion resistance means that it wont degrade quickly, even in harsh environments, translating into fewer applications and repairs.
Reduced Downtime and Increased Productivity
Maintenance and repairs are inevitable in any manufacturing environment, but aluminum framing helps minimize downtime. The frames are easy to assemble and dismantle, enabling quick adjustments, repairs, or replacements. This ensures that operations can continue smoothly without significant interruptions.
Sustainability
Aluminum is 100% recyclable, making it an environmentally friendly choice in an era where sustainability is becoming increasingly important in all industries, including aerospace. Recycling aluminum saves energy and resources, aligning with the industry’s sustainability goals.
Aerospace Industry Trends
As aerospace technology advances, the industry’s need for efficient, adaptable, and sustainable solutions is growing. Here are some trends that are further increasing the demand for aluminum framing in aerospace:
Automation and Robotics Integration
The rise of automation and robotics in aerospace manufacturing has led to to the need for equipment and workstations that can support robotic arms and other automated systems.
Lightweight and Fuel-Efficient Components
With the aerospace industry’s ongoing push towards lighter, more fuel-efficient designs, aluminum framing’s lightweight properties make it an attractive choice. This trend is evident not only in assembly and support structures but also in the framing of specialized aerospace machinery and tools.
Increased Focus on Safety and Ergonomics
Worker safety and ergonomics are top priorities in aerospace. Aluminum framing supports this trend by enabling the construction of safe, customized workspaces and platforms, which can be adjusted to meet the ergonomic needs of workers, ultimately reducing injury risk and improving productivity.
Sustainable Manufacturing Practices
As aerospace companies increasingly focus on sustainability, aluminum framing stands out due to its recyclability. Using aluminum framing aligns with aerospace companies’ goals to reduce their environmental impact by employing sustainable materials and practices throughout their manufacturing processes.
Future Outlook
As the aerospace industry continues to evolve, aluminum framing is poised to become even more integral. The development of new aluminum alloys and enhanced manufacturing processes is expected to improve the strength, durability, and performance of aluminum framing even further. With emerging technologies like 3D printing, there may soon be even more advanced customization options for aluminum frames, allowing for faster, and more efficient production.
Additionally, as the industry explores new frontiers such as space tourism and deep-space exploration, the demand for lightweight, modular, and durable solutions like aluminum framing is likely to surge. Companies involved in space exploration and aerospace manufacturing are already testing and implementing aluminum framing in novel ways, pushing its potential to new heights
Conclusion
In conclusion, aluminum framing has become a crucial part of aerospace because of its strength, flexibility, durability, and eco-friendly qualities. It’s used in everything in workstations and platforms to custom storage and safety barriers, showing just how adaptable and essential it is in the industry. As aerospace companies continue to grow and innovate, aluminum framing will keep supporting better assembly processes and sustainability goals. With ongoing advancements in aluminum technology, the future holds even more possibilities for its use, further cementing its importance in aerospace.
For aerospace companies looking to improve assembly lines and layouts, Pacific Integrated Handling’s Aerospace Applications and Aerospace Catalog offer expert insights and high-quality solutions tailored to industry needs. Contact us to learn how our aluminum framing solutions can make a difference in your operations.